Do you want to know more about core drills? At Excision, we understand that customers often have questions about these versatile cutting tools. So, we've put together a list of five common queries to help you understand core drills better and see how they can benefit you. Sound good? Let's dive in.
Here’s what we’re going to be discussing in this article:
-
What is a core drill?
-
Why is a core drill better than a jobber drill?
-
What causes dull or broken core drills?
-
What is a pin?
-
Do I have to use coolant?
What is a core drill?
A core drill is a specialised tool for drilling through steel. Similar to a hole saw for wood, a core drill only cuts the outside edge of a hole.

It produces accurate burr-free holes to close tolerances without pre-drilling or step drilling. It can drill a much larger hole and requires less force and time than a standard twist drill bit. As it turns, the drill produces chips from the outside cutting edges and after cutting the hole a ‘slug’ (a round chunk of steel from the centre of the cutter) falls out.
Why is a core drill better than a jobber drill?
You may have wondered “What’s the advantage of using a core drill?” If that’s the case, it’s because they simply have superior hole-making capabilities.
They can cut faster because they cut out a circle, rather than a hole. This same reason means that they have to do less work in every cut, meaning that they last longer, and drill holes with less power and torque. They also produce a better finish that is burr-free. However, one of the most important factors is they produce a round hole with very tight tolerances. This is because the structure of the drill provides less room for movement during the cut. In addition, core drills can be resharpened.
By their very nature, twist drills are only designed to drill very small holes. This is because their angled cutting edge slopes downwards towards the centre. This is necessary not only to provide stability through a centre point, but to allow it to cut.
However, as the twist drill spins, the cutting edges move at different speeds (see diagram below). The outside edge is moving faster than the centre (nearly a velocity of zero). This means that the outside edge is working harder than the inside edge, resulting in inconsistent removal of material that makes the drill work harder and slower.
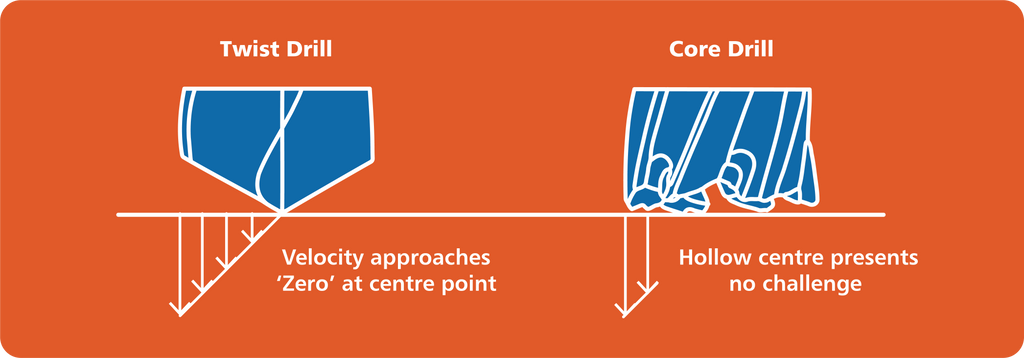
On the other hand, with core drills the speed of the cutting edge is consistent, presenting no challenge to either the speed or ease of drilling.
What causes dull or broken core drills?
Dull or broken cutters are a common source of frustration with core drill users. It can be caused by multiple things.
One cause of broken or prematurely dull core drills is a feed rate that is incorrect. To extend the life of your drill, you need to use the optimum feed rate for the material you’re cutting, the diameter of the cutter and the type of cutter. You should also maintain a firm and steady feed pressure during the cut to optimize performance. You’ll know you’re doing it correctly if you can hear the drill motor working and see long, stringy chips being pulled from the hole, forming a bird's nest around the cutter.
On the other hand, if there are blue or purple chips while you’re cutting, it means that you’re not using enough coolant, or you’re pushing too hard.
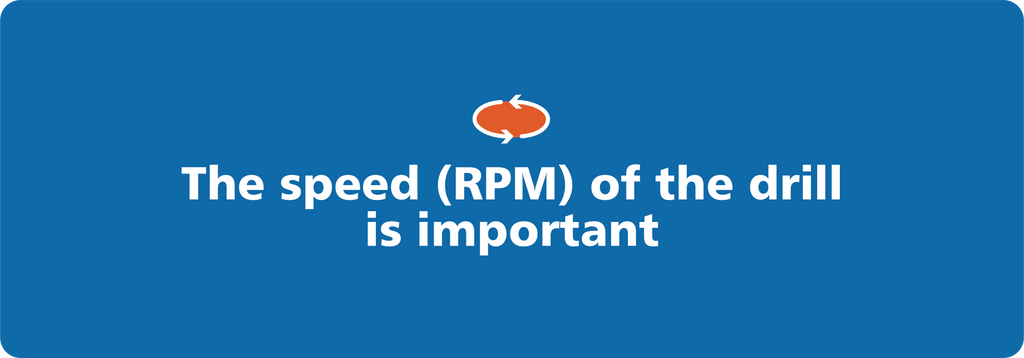
However, even more important is the speed (RPM) of your magnetic based drill. This is where a variable speed drill is important, as different sized cutters shouldn’t be run at the same speed. Essentially, the bigger the diameter of the core drill, the faster the speed at the outside of the drill where the cutting is happening. If, for example, you shifted from a 22mm diameter cutter to a 50mm cutter and kept the RPM the same, you’re going to be running it too fast, breaking or dulling the drill.
If you’re not sure what speed you should be running your core drills at, you can download our handy guide to find out exactly what speed you should be running your drills at for both HSS-Co and TCT cutters.
What is a pin?
A Pin is a large pencil-looking object that must be used when using a core drill. Pins go through the centre of the cutter, retracting up into the magnetic drill arbour as the hole is made. These ejector pins last a long time and can be used with multiple sizes of drills.
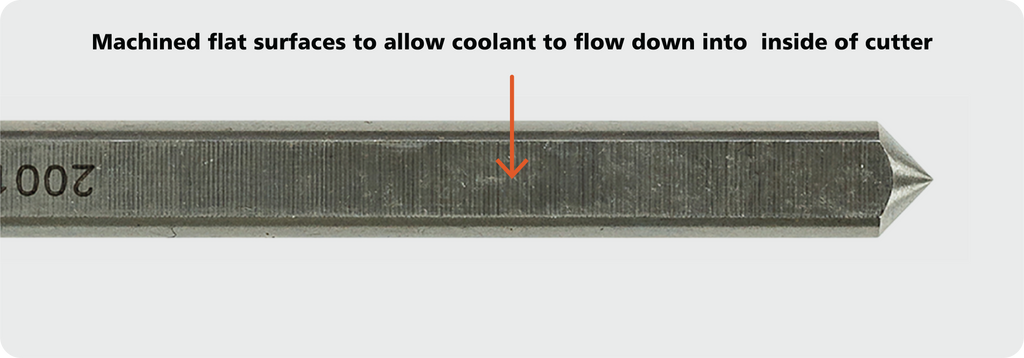
They serve three important functions:
- Eject the slug at the end of the cut
- Locate the centre of the hole
- Allow coolant to flow down around the slug and to the cutting teeth
Do I have to use coolant?
The short answer is yes, you should be using coolant with your core drills. That’s because coolant increases the tool life of a core drill dramatically. Coolant removes heat from the cut, but more importantly provides lubrication, reducing friction and allowing the cutting edge to remain sharp and efficient.
There are many different types of lubricants available, depending on the application. To get the best results always use the coolant system on your magnetic drill. Spraying or squirting coolant at the drill while it is turning reduces its effectiveness, as the coolant is pushed aside by the chips and flutes before it reaches the core drill. That’s why we’d recommend you use internal cooling, because it gets spun by centrifugal force right to the tooth tip on the cutter.
That’s it! If you have any more questions regarding core drills, feel free to reach out to our team.